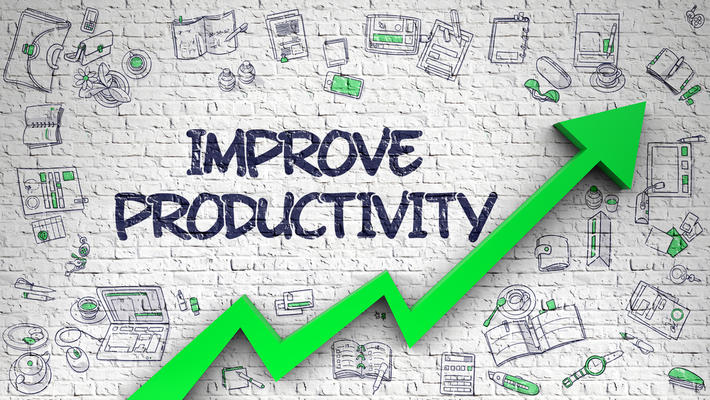
Produktivität und Effizienz des Druckgusses steigern
Angesichts des zunehmenden globalen Wettbewerbs, der die Suche nach Verbesserungen der Produktionseffizienz vorantreibt, spricht die Ultraseal International Group darüber, wie Innovationen bei Trennmitteln und Sprühtechnologie die Industrie dabei unterstützen können, Produktivität, Effizienz und Wettbewerbsfähigkeit zu verbessern.
In der heutigen Druckgussindustrie sind die Steigerung der Produktivität, die Optimierung der Kosten und die Qualität der Produktion Schlüsselfaktoren, insbesondere angesichts des zunehmenden globalen Wettbewerbs und der Notwendigkeit, immer komplexere Komponenten herzustellen. Insbesondere diese Faktoren haben die Gießereien dazu veranlasst, nach neuen Lösungen zu suchen, die die Herstellung hochwertiger Gusskomponenten ermöglichen, die Kosten senken und die Herstellungsprozesse verbessern. Die Entwicklungen in der Automobilindustrie haben zu einer Verlagerung des Druckgusses hin zu komplexeren und leichteren Komponenten im Antriebsstrang, im Fahrgestell und in den Bauteilen geführt. Das Wachstum des Rahmens und insbesondere der Struktur hat zu Investitionen in größere Druckgussmaschinen und teurere Werkzeuge geführt. Diese Entwicklung hat anschließend alle Aspekte der Druckgussvorgänge hervorgehoben, einschließlich der Rolle des verwendeten Trennmittels, da die Hersteller versuchen, die Produktivität der Druckgussindustrie zu steigern, die Prozesszuverlässigkeit, die Ausgabequalität zu verbessern und zu steigern Dauer der Form.
Um zu verstehen, wie die Auswahl von Trennmitteln erheblich zur Verbesserung der Produktionseffizienz, Kostensenkung und des Geschäftserfolgs beitragen kann, müssen wir uns die Vorteile ansehen, die neue Technologien bieten.
Maximieren Sie die Abdeckung effektiv, um die Produktivität der Druckgussindustrie zu steigern
Wenn wir an den Hauptzweck von Trennmitteln denken - die Freisetzung sauberer Teile zu erleichtern und das Schweißen von Formen zu vermeiden -, ist eine gleichmäßige Abdeckung wichtig, um die Produktion zu steigern, die Zuverlässigkeit des Prozesses und die Gesamtqualität des Endprodukts zu verbessern. Die Verwendung herkömmlicher Schmiermittel auf Wasserbasis führt zur Verdunstung von Flüssigkeiten, wenn diese mit den heißen Stahlformen in Kontakt kommen, wobei eine Menge geschmierter Beschichtung zurückbleibt.
Dies ist ein kritischer Schritt, da ein Überschuss an Schmiermittel nicht zulässt, dass Flüssigkeiten schnell genug verdampfen, wenn das Metall eingespritzt wird. Eine unzureichende Menge an Schmiermittel kann jedoch zu einem schlechten Materialfluss oder einem schlechten Schweißen der Form führen, was zu Oberflächenfehlern und Porosität führt und die Gesamtqualität des Teils beeinträchtigt. Da die Industrie bestrebt ist, die aktuelle Nachfrage nach komplexen einteiligen Bauteilen zu befriedigen, wird dieses Problem aufgrund der Komplexität der Form immer konsistenter, da eine gleichmäßige Schmiermittelabdeckung über die gesamte Form erreicht werden muss. Formen haben Hohlräume, in denen typischerweise übermäßige Mengen an Schmiermitteln auf Wasserbasis verbleiben, was zu Kaltflüssen, Porosität und Flecken auf der Gussoberfläche führt.
Die Lösung für dieses Problem liegt in der elektrostatischen Sprühtechnik. WFR-EC wurde von Lubrolene entwickelt und verfügt über eine elektrostatische Aufladung des Trennmittels, die bei Anwendung über eine speziell entwickelte elektrostatische Spritzpistole einen umhüllenden Effekt erzeugt und eine gleichmäßige Abdeckung der Trennmittel unabhängig von der Komplexität der Form garantiert. Die Anwendung von Lubrolene WFR-EC durch ein elektrostatisches Sprühen reduziert Schweißprobleme weiter und erleichtert das Entfernen des Gleitmittels auf Wasserbasis, um höhere und konstantere Qualitätsniveaus bei Druckgussbauteilen sicherzustellen.
Die Summe der elektrostatischen Aufladung mit Lubrolene WFR-EC verbessert auch die Haftungseigenschaften erheblich und sorgt für eine gleichmäßigere Ölmembranbildung, die für eine gleichmäßige Formbedeckung und eine gleichmäßige Freisetzung wesentlich ist. Zusätzlich zu den Vorteilen in Bezug auf die Qualität führen höhere prozentuale Haftungsgrade zu einer Verringerung des Materialabfalls und zu verbesserten Zykluszeiten.
Normalerweise erreicht das Auftragen eines Trennmittels auf Wasserbasis mit einer Luftspritzpistole nur eine Adhäsionseffizienz von 4%. Die Verwendung der speziell von Lubrolene entwickelten Spritzpistolen-Technologie verbessert stattdessen die Anwendung von Lubrolene WFR-EC und erreicht eine Haftungseffizienz von mehr als 80% im Vergleich zu herkömmlichen Schmiermitteln auf Wasserbasis.
Die Prozessgeschwindigkeit steigt mit der Sprühzeit, um die Produktion zu steigern
Bei dem Versuch, die Produktion zu steigern und die Effizienz eines Prozesses zu verbessern, ist es oft leicht, Schritte zu übersehen, die immer auf eine bestimmte Weise ausgeführt wurden. Beim Druckguss ist der Einsatz von Schmiermitteln einer dieser Fälle. Als kurzer und sich wiederholender Zyklus kann die Einsparung einiger Sekunden im Druckgussprozess zu erheblichen Zeiteinsparungen und direkten Auswirkungen auf Produktivität und Kosten führen, solange das Werkzeug entsprechend ausgelegt ist. Wenn wir die Standardausrüstung für die Luftsprühanwendung einhalten, um eine vollständige Abdeckung und eine gute Haftung der Form zu gewährleisten, muss dieser Werkzeugtyp aus mehreren Winkeln sprühen. In der Praxis nimmt die Verwendung dieses Geräts Zeit in Anspruch und kann die Qualität bei ungleichmäßigen Abdeckungsgraden beeinträchtigen, insbesondere bei komplexeren Modulen. Durch elektrostatische Anziehung kann die Lubrolene-Pistole jedoch einen viel größeren Bereich abdecken und gleichmäßig daran haften, ohne dass aus verschiedenen Winkeln gesprüht werden muss. Mit einer typischen Sprühzeit - selbst für Maschinen mit mehr als 4000 Tonnen - von wenigen Sekunden kann mit speziell entwickelten Lubrolene WFR-EC-Sprühköpfen und Sprühköpfen die Sprühzeit erheblich verkürzt werden. Dies führt zu einer Verkürzung der Zykluszeiten, einer Ertragssteigerung und einer Produktivitätssteigerung. Darüber hinaus kann die modular aufgebaute Lubrolene-Spritzanlage problemlos für Druckgussmaschinen jeder Größe eingesetzt werden. Das wartungsarme Design verbessert die Zuverlässigkeit und bringt potenziell erhebliche Vorteile für die Druckgussindustrie.
Erhöhen Sie die Betriebszeit und senken Sie die Kosten durch erhöhte Werkzeugfestigkeit
Eine schnelle Maximierung der Formbedeckung kann den Herstellern helfen, ein höheres Maß an Effizienz zu erzielen und die Produktivität zu steigern. Die Verwendung von Lubrolene WFR-EC bietet jedoch einen zusätzlichen Vorteil, der möglicherweise die wichtigsten Ergebnisse liefert: eine längere Standzeit. . Die Verwendung herkömmlicher Trennmittel auf Wasserbasis ermöglicht ein schnelles Abkühlen der Formoberfläche, was zu extremen Temperaturschwankungen führt, die aufgrund wiederholter Druck- und Zugspannungen schnell zur Bildung von Rissen auf der Formoberfläche führen können. Mit Rissen, die sich typischerweise nach hundert Hüben zu bilden beginnen, wird die Werkzeuglebensdauer verringert und die weniger verfügbaren Hübe betragen etwa 120.000 in einer typischen Druckgussmaschine.
Dank seiner sehr geringen Sprühmenge wird der bei herkömmlichen Verfahren vorherrschende schnelle Kühleffekt bei Verwendung von Lubrolene WFR-EC erheblich verringert, wodurch die thermischen Belastungen, denen die Matrizen normalerweise ausgesetzt sind, nahezu beseitigt werden. Durch die bis zu sechsfache Verlängerung der Lebensdauer des Werkzeugs kann die Kostenreduzierung 500.000 € pro Jahr übersteigen. Die längere Lebensdauer der Geräte erfordert auch weniger Werkzeuge und bietet weitere Einsparungen bei den Arbeitskosten von bis zu 20%. Insgesamt hilft Lubrolene WFR-EC den Herstellern, die Produktion in der Druckgussindustrie zu steigern, effektiver zu arbeiten, die Produktionseffizienz zu verbessern, die Kosten zu senken und die Produktion komplexerer Komponenten zu ermöglichen, die den Anforderungen der Branche entsprechen. . Eine höhere Spritzapplikationsgeschwindigkeit bedeutet eine signifikante Verkürzung der Zykluszeit; Eine gleichmäßigere Haftung führt zu einer höheren Prozesssicherheit und reduziert den Materialabfall. und die Verringerung der Belastung der Formen erhöht ihre Dauer und Beständigkeit im Laufe der Zeit erheblich. Die Ergebnisse dieser grundlegenden Vorteile liegen auf der Hand. Sie verbessern die Produktivität und führen zu einer Kostensenkung für die Hochdruckgussindustrie, ohne die Qualität ihrer Produktion zu beeinträchtigen.