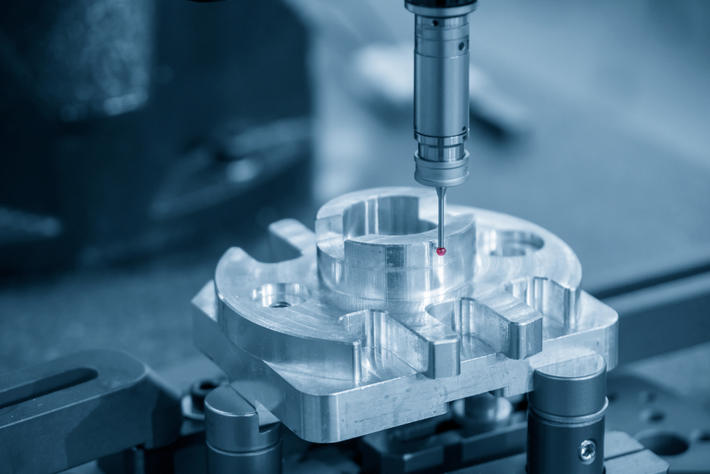
Foundry 4.0, IoT steigert die Produktivität
Die Metallurgie investiert in 4.0-Technologien und -Anlagen. Dank IoT steigt die Effizienz: Die von den Sensoren gelieferten Informationen schlagen Änderungen vor, um den Produktionsprozess und die Wartungsverfahren zu verbessern und den Energieverbrauch zu senken. Alles ohne die Qualität der Arbeit aus den Augen zu verlieren.
Unternehmen des Metallurgiesektors, von Eisen- und Nichteisengießereien bis hin zu Stahlproduzenten, investieren, um die Wettbewerbsfähigkeit auf dem Markt zu verbessern: Trotz der schwierigen Zeit stellen sich die fortschrittlichsten Unternehmen der Zukunft mit neuen Anlagen in Industrie 4.0-Logik, um Innovationen in die Industrie einzuführen Fabrik, Steigerung der Produktivität und Sicherheit des Personals.
Die Gießerei 4.0 und die Produktivitätssteigerung
Die von 4.0-Unternehmen generierte Datenökonomie ermöglicht es auch, die Wartung von Maschinen zu verbessern, ein entscheidendes Merkmal in einer von kontinuierlichen Prozessen geprägten Branche, und den Energieverbrauch besser zu steuern, ein Aspekt, der in einer energieintensiven Branche keineswegs zu vernachlässigen ist.
In der Metallindustrie werden mehrere 4.0-Experimente durchgeführt, wie z. B. die Studien, die auf diesem Gebiet vom RAS-Team (Applied Research and Sustainability) des Multisektoralen und Technologischen Servicezentrums (CSMT) von Brescia (www.Csmt.it) durchgeführt wurden.
Im Hinblick auf die Erneuerung und Aktualisierung mit Sensoren und Software von mehr oder weniger veralteten Maschinen, die so mit der Digitalisierungslogik 4.0 kompatibel gemacht werden, haben sich die Brescia-Forscher ein Ziel gesetzt: Anwendungen zu entwickeln, die der Verbindung zwischen Fabrikmaschinen und Informationssystemunternehmen gewidmet sind, mit dem Ziel, kritische Informationen über Produktionsprozesse verfügbar zu machen, die Produktivität zu steigern und Steuervergünstigungen für Super-Hyper-Abschreibungen zu erhalten.
In diesem Zusammenhang hat das Technologiezentrum einen innovativen Algorithmus zum Wiegen des wichtigsten Rohstoffs für Gießereien entwickelt. Es ist der Metallschrott, der in diesem Fall von einem Hallenkran transportiert wird, der effektiv und genau quantitativ gemessen werden kann. Auf diese Weise profitieren sowohl die Bewirtschaftung des Schrottplatzes als auch das Endverarbeitungsprodukt davon. Die Genauigkeit der Messungen überstieg 98 %; während Pausen und Ineffizienzen konsequent reduziert und erhebliche Einsparungen in den Kontrollphasen der fertigen Produkte erzielt wurden.
Die Kraft des maschinellen Lernens in der 4.0-Foundry
Natürlich ermöglicht eine solche evolutionäre Initiative die Ausweitung auf andere Teile des Produktionszyklus, wodurch eine sorgfältigere und effektivere Überwachung gewährleistet wird. Daher hat die RAS auch ein Sensorisierungsprojekt für die Wagen entwickelt, die zur Ölversorgung der Maschinen verwendet werden. Das Ziel ist hier die Sammlung und Verarbeitung von Daten über den Ölverbrauch jeder Station des Produktionsprozesses mit der LoraWAN-Funktechnologie. Mit derselben Technologie wurden alte Schmelzöfen für Aluminium nachgerüstet, um eine optimale Temperaturkontrolle zu erreichen. Und nicht zuletzt war am CSMT auch die Integration eines Nervenzentralennetzwerks von Sensoren zur Erfassung von Prozessdaten an bestehenden Maschinen geplant.
Die Perspektive ist die Überwachung und Analyse der für ein Unternehmen interessanten Größen im Kontext von vorausschauender Wartung und Diagnose unter Verwendung von Techniken der künstlichen Intelligenz und des maschinellen Lernens.
Neue Managementsysteme Industrie 4.0 und das IoT haben die Innovationskraft der metallurgischen Industrie beschleunigt. Dank dieser beiden Faktoren konnten neue Managementsysteme entwickelt werden, die neben einer deutlich verbesserten Qualitätsüberwachung eine Kombination aus vorbeugender und vorausschauender Wartung schaffen konnten, die eine deutliche Produktivitätssteigerung für die Gießerei 4.0 ermöglichte.
Die Informationen zu Maschinenpausen und -laufzeiten, zu den unterschiedlichen Produktionsarten sowie zu Qualität und Kosten des Produkts wurden mit den Daten der in der gesamten Produktionskette eingesetzten Sensoren abgeglichen, um unerwartete Zusammenhänge aufzudecken und schlagen Änderungen an normalen Routinen innerhalb des Produktionsprozesses vor.
Die günstigsten Investitionen für Industrie und Gießerei 4.0
Diese Strategien wurden bereits in der Vergangenheit getestet, aber erst in jüngster Zeit wurden Investitionen durch die extreme Verbreitung von Kontrolle und die Verwaltung von Big Data erschwinglich.
Ein Beispiel dafür wurde im letzten Jahrzehnt von den Forschern V.R. Radhakrishnan und A.R. Mohamed wendet die Soft Sensors, also eine Software, in der verschiedene Messungen zusammen verarbeitet werden, um andere Größen zu berechnen, zur Überwachung des Schmelzprozesses an; Tatsächlich war die Kontrolle dieser Phase aufgrund der mit dem Prozess verbundenen Probleme immer eine große Herausforderung. Insbesondere konzentrierten sich die beiden Gelehrten auf die Messung der Zusammensetzung des geschmolzenen Metalls; Normalerweise würden diese Analysen spektrografische Techniken erfordern, die nur offline durchgeführt werden können, aber dank der Verwendung von Software auf der Grundlage neuronaler Netze konnten die Autoren ein Modell entwickeln, das 33 Prozessvariablen in Beziehung setzt, einschließlich der Menge an geschmolzenem Metall, Schlacken und deren Zusammensetzung mit allen für Legierungen wichtigen Bestandteilen einen Fehlerwert von weniger als 3 % erreicht.
Die intelligenten Komponenten der Gießerei 4.0
Andere einfachere Anwendungen dieser Technologien im metallurgischen Sektor wurden durch die Einführung von Komponenten ermöglicht, die bereits in der Fabrik über Datenabruf- und -übertragungssysteme verfügen, nämlich intelligente Komponenten. Diese ermöglichen von der ersten Installation an einen konstanten Datenfluss während der gesamten Nutzung und erleichtern die Digitalisierung des Unternehmens dank ihrer einfachen Installation erheblich, da sie keine fundierten Kenntnisse aller seiner Erkennungssysteme erfordern, um zu funktionieren.
Ein Anwendungsbeispiel, das sich in Betrieben verbreitet, die mit Durchlauföfen arbeiten, ist der Einsatz von automatischen Türen, die das Vorhandensein von Halbzeugen in der Nähe der Öfen erkennen, ihre Form und Position analysieren und ihre Güte feststellen, bevor sie die Behandlung durchführen; Auf diese Weise können Sie alle Produkte aussortieren, die nicht den gewünschten Standards entsprechen, und die Öffnungs- und Schließzeiten der Ofentür verbessern, um weniger Wärme abzugeben und Energie zu sparen.
Dieselben Detektionssysteme, mit denen die smarten Komponenten ausgestattet sind, können einen doppelten Zweck haben: die oben erwähnte Analyse der äußeren Bedingungen und die Berechnung der verbleibenden Nutzungsdauer der Komponente (RemainingUsefulLifetime) durch die Untersuchung von Belastungen wie Spannungen, Vibrationen und Temperaturen. unterworfen. Die Schwankungen dieser Daten liefern eine wichtige Alarmglocke im Hinblick auf die vorausschauende Wartung der Anlagen und die Qualitätskontrolle der Gießerei 4.0. Beispielsweise könnte die Erfassung des Temperaturanstiegs durch die Handhabungskette einer metallurgischen Endloslinie mit der Bildung massiverer Stücke als üblich oder mit einem erheblichen Fehler bei der Formung der Legierung mit entsprechender Änderung der Temperaturleitfähigkeit zusammenhängen. Wenn die Bewegungskette selbst einen Spannungsanstieg im Vergleich zu den normalerweise ausgesetzten Spannungen aufweist, könnte dies ein Zeichen für eine Fehlfunktion der Maschine sein.
Einigkeit ist Stärke, auch in der 4.0-Gießerei
Die Kenntnis dieser Informationen, die im Einzelfall betrachtet irrelevant erscheinen mag, da vielleicht ein wenig außerhalb der klassischen Standards, einem spezialisierten Analysemodell anvertraut, zur Erkennung und Vermeidung erheblicher Schäden führen kann.
Um die Anwendung von datenwissenschaftlichen Technologien auf metallurgische Prozesse zu fördern, hat die Europäische Gemeinschaft bereits 2018 große Mittel für die Forschung bereitgestellt, die von einer italienischen Exzellenz, der Universität Sant'Anna von Pisa, abgefangen wurden, die Vorhersagemodelle entwickelt hat wie:
- CyberMan4.0, das darauf abzielt, die vorbeugende Wartung und ihre Weiterentwicklung zur vorausschauenden Wartung zu verbessern;
- TrackOpt, das auf die Implementierung eines Pfannenverfolgungssystems für alle Stadien abzielt, um die Logistik zu optimieren.
Die Prototypversionen dieser Systeme wurden in verschiedenen großen Industrieunternehmen getestet. Da die Modelle die Verwendung von sensorisierten Komponenten und Software beinhalten, die in der Lage sind, Informationen während der Produktion online zu sammeln, haben andere Unternehmen in Erwartung zukünftiger Investitionen begonnen, sich in Richtung Digitalisierung und Datenerfassung zu bewegen.
Auch der Gigant Microsoft hat mit seiner Azure-Plattform erste Ergebnisse im Bereich der Big-Data-Analyse für die Prävention, Vorhersage und Qualität von Hüttenwerken gebracht.
Die Rolle des Komponentenlieferanten in der Gießerei 4.0 liegt in der Steigerung der Produktivitäz
Eine komplexe Tätigkeit wie die Konstruktion metallurgischer Anlagen kann bei Komponentenlieferanten wertvolle Unterstützung finden. Die in Gießereien eingesetzten Maschinen erfordern robuste, langlebige Komponenten, die einfach und komfortabel zu montieren und zu warten sind. In diese Richtung müssen Zulieferer eine breite Produktpalette entwickeln: vom Lamellengelenk bis zum Elastomergelenk, vom Kugelzahngelenk bis zum modularen Drehmomentbegrenzer. Alle Komponenten, die sich in ein intelligentes Gelenk verwandeln lassen, wurden für die Montage an 4.0-Maschinen konzipiert und entwickelt.
Die Entwicklung intelligenter Komponenten, die mit integrierten Sensoren ausgestattet sind, die während ihres Betriebs Daten messen, sammeln und übertragen können, steht in vollem Einklang mit den Prinzipien der vierten industriellen Revolution: Die Gelenke müssen in der Lage sein, sich selbst zu überwachen und jede Art von Aktivität unverzüglich zu melden Störungen oder Fehlfunktionen, die die Produktion beeinträchtigen könnten - ein großer Vorteil für preisbewusste Hersteller.
Quelle: A&L Aluminium Alloys Pressure Diecasting Foundry Techniques