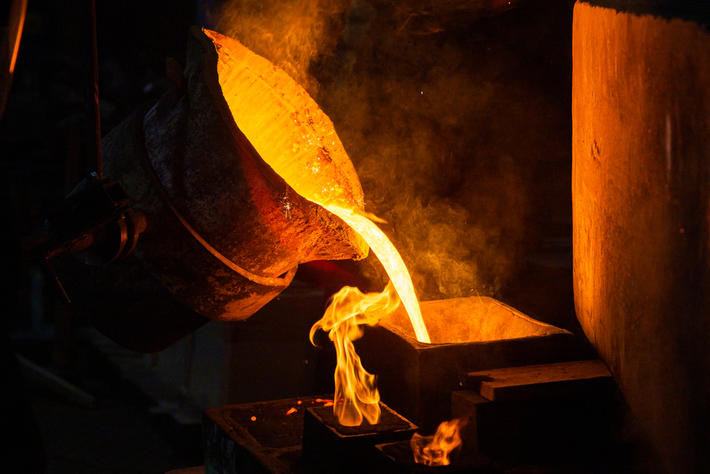
Erste industrielle Produktion ZnAl15Cu1Mg
Seit 2014 im Rahmen des UNIBS & Partner-Projekts mit der Region Lombardei die ersten Warmkammer-Druckgusstests mit dem übereutektischen ZnAl15Cu1Mg durchgeführt wurden, wurden zahlreiche Tests durchgeführt, um die verschiedenen Probleme bei der Entwicklung einer Druckgussmaschine zu bewältigen Druckguss in einer zum Gießen der Legierung geeigneten Warmkammer.
Im Jahr 2018 führte Studio Olafur Eliasson nach der Wiederaufnahme des Projekts zum Warmkammer-Druckguss von ZnAl15Cu1Mg den endgültigen Machbarkeitstest in einem künstlerischen Projekt von MORI (WT) in Tokio durch. Die Wahl einer Zinklegierung entstand aus der Idee, das Hauptmetall Zink aus häuslichem Verbrennungsstaub zurückzugewinnen.
Da es sich bei dem Kunstwerk um ein mehrvolumiges, von der Decke hängendes Objekt handelt, das erdbebensicher sein muss, wurden zahlreiche mechanische Simulationen durchgeführt, die den Bedarf an einer Legierung mit besserer Leistung in Bezug auf viskoses Fließen (oder Kriechen) und mechanischen Widerstand verdeutlichten. Daher fiel die Wahl auf die Verwendung der ZnAl15Cu1Mg-Legierung anstelle der klassischen Zinklegierung für den Druckguss.
Nach Überprüfung der Stabilität der Legierung in der Warmkammer-Druckgussmaschine wurde eine Reihe mechanischer Testproben gegossen, um deren Gesamteigenschaften zu überprüfen. In einer weiteren Serie wurde die Recyclingfähigkeit der Legierung nachgewiesen, so dass normale Produktionsläufe erreicht werden konnten.
Der Guss der Kerne des Kunstobjekts verdeutlichte die Möglichkeit, den Anwendungsbereich der in einer Warmkammermaschine gegossenen Zinklegierung zu erweitern.
Einführung in die industrielle Produktion von ZnAl15Cu1Mg
Seit 2018, nach vier Jahren intensiver Tests der Leistung der ZEP® 1510-Legierung unter verschiedenen Bedingungen in der Warmkammer-Druckgussmaschine, wurde beschlossen, das geeignete Projekt zu identifizieren, um eine komplette Industrieserie zu starten. Dies wurde in Verbindung mit einem Kunstprojekt des Berliner SOE Art & Design Studios erreicht, bei dem eine Serie von vier Druckgussskulpturen geschaffen wurde, die von der Decke eines Gebäudes in Tokio, Japan, hängen. Die Skulpturen bestehen aus 7000 elfseitigen Körpern. Die einzelnen Körper bestehen aus Druckguss und sollten aus einer recycelten Zinklegierung bestehen, die durch Elektrolyse von Zink gewonnen wird, das aus dem Staub der Hausmüllverbrennung gewonnen wird.
Ergebnis des Warmkammer-Druckgusses von Zink und Aluminium
Da das Kunstwerk von der Decke hängt, sind Aspekte wie das Gewicht äußerst wichtig bei der Auswahl der Legierung für den Druckguss. Der klassische ZL5 (Zamak5) hat eine Dichte von ca. 6,7 g/cm³, sodass die Skulptur unter ihrem Eigengewicht zähflüssiges Gleiten erfahren kann. Aus diesem Grund wurde die neue Legierung ZEP® 1510 gewählt, die das Gewicht um ca. 20 % reduziert und eine 100-fach höhere Kriechfestigkeit bei Raumtemperatur aufweist. Die Verbesserung der mechanischen Beständigkeit (20 % mehr als bei Zamak 5) würde es den Designern auch ermöglichen, das Konzept zu erweitern.
Bevor die Serie erstellt werden konnte, waren jedoch noch weitere Prüfungen in der Gießerei erforderlich, darunter:
- Die Stabilität der Legierung während einer längeren Gießzeit;
- Die tatsächlichen mechanischen Eigenschaften der Legierung, um ihre Stabilität während der Alterung sicherzustellen;
- Die Recyclingfähigkeit der Legierung, was die Wiederverwendung der Gusskanäle und der Gussgrate impliziert.
Diese drei Gussserien wurden im Labor der Oscar Frech GmbH durchgeführt.
Zuerst auf einer kleinen französischen W20-Warmkammer-Druckgussmaschine mit einer 12-fach-Kokille, um die Gießbarkeit der Legierung zu überprüfen und die Grenzeinstellung der Parameter zu ermitteln. Es wurde schnell klar (insgesamt 5000 Injektionen in einer Gusswoche), dass die Gusstemperatur auf 530 °C erhöht werden musste, um die Legierung ausreichend flüssig zu machen und eine gute Füllung des Hohlraums zu ermöglichen.
Gleichzeitig wurde die Recyclingfähigkeit anhand von drei Gewichtsverhältnissen zwischen Neu- und Recyclingmaterial (25 % / 50 % und 100 % Recyclingmaterialanteil des Gussteils) überprüft. Obwohl die Legierung stabil bleibt, steigt Fe aufgrund der Verunreinigung des Tiegelinhalts an, wenn eine bereits recycelte Legierung mit einem größeren Fe-Anteil eingeführt wird. Die Analysen wurden mittels Spektralanalyse bei der Grillo Werke AG an Proben durchgeführt, die an verschiedenen Stellen des Tiegels entnommen wurden.
Die zweite Serie wurde auf einer Heißkammer-Druckgussmaschine Frech W80 durchgeführt, um eine ausreichende Anzahl mechanischer Proben (2000 Injektionen) zu gießen, um eine genaue Überprüfung der mechanischen Leistungen zu starten und sie mit dem normalen Druckgussmaterial zu vergleichen in der Heißkammer Zamak 5.
Die mechanischen Eigenschaften der 3 mm flachen Proben (UTS/R0,2 %/E-Modul/Dehnung) wurden mit der Legierung im gegossenen Zustand überprüft, künstlich gealtert (2 Stunden bei 105 °C) und einer Wärmebehandlung (4 Stunden) unterzogen bei 150°C) im Vergleich zu den gleichen Eigenschaften wie Zamak5. Gleichzeitig zeigte die Überprüfung der Eigenschaften während der natürlichen Alterung eine moderate Alterungstendenz im Vergleich zur bekannten von Zamak 5. Die Alterung von ZEP® 1510 über die letzten 3,5 Jahre erscheint linear.
Die Analyse ergab daher, dass die Legierung stabil genug ist, um mit den 10.000 Injektionen zu beginnen, die erforderlich sind, um das für die Körper des SOE-Kunstwerks erforderliche Volumen zu erhalten.
Die Serie wurde auf Frech W125 mit Doppelhohlraumform gegossen. Die Gießbedingungen wurden auf eine Temperatur von 530 °C für den Tiegel und 170 °C für die Form eingestellt, wobei die Einspritzgeschwindigkeit an der Mündung der Hohlräume 40 m/s erreichte. Dies geschah gleichzeitig mit der Wiederverwertung der Angüsse. Um den Temperaturverlust zu begrenzen, war es notwendig, die Angüsse so schnell wie möglich zu schneiden, um die Restwärme zurückzugewinnen. Gleichzeitig wurde die Stabilität der Legierung durch die Entnahme von drei Proben pro Tag überprüft, um die Qualität des Gussprodukts zu gewährleisten. Der gesamte Guss der Serie würde über sechs Wochen dauern und würde auch die Aggressivität der Legierung in Bezug auf Tiegel, Schwanenhals, Kolbenringe und alle Geräte, die im betrachteten Zeitraum in die Legierung eingetaucht waren, anzeigen.
Die Studie bestätigte die Stabilität des in der Legierung selbst enthaltenen Legierungselements Al und zeigte, dass letztere ohne besondere Zersetzungsrisiken für Heißkammergeräte verwendet werden kann und geeignet ist.
Die erste Serie von Gussprodukten auf einer Warmkammer-Druckgussmaschine zeigte, dass die ZEP® 1510-Legierung industriell einsetzbar ist. Die Legierung bleibt stabil, solange alle in den Tiegel eingetauchten Teile mit Keramikfarbe geschützt werden. Die Gummibänder gelten als Verbrauchsmaterial und haben eine Lebensdauer von ca. 1000 Injektionen. Die hohe Schmelztemperatur der Legierung im Tiegel erfordert ein leistungsstarkes Heizsystem, um den notwendigen Wärmeeintrag zum Schmelzen der Legierungsbarren und zur Aufrechterhaltung der Produktion zu gewährleisten.
Quelle: In Fonderia – ll magazine dell’industria fusoria italiana