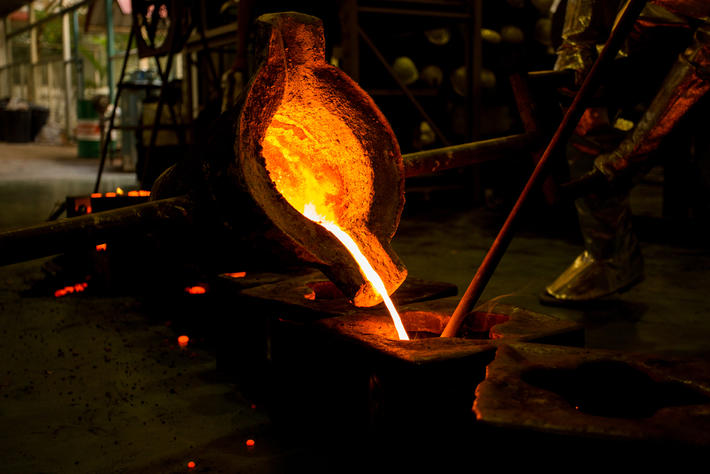
Die Dekarbonisierung von Gießereien: neue Ziele für maximale Umweltverträglichkeit
Trotz der komplizierten wirtschaftlichen Situation der letzten Jahre haben Unternehmen weiter investiert, um den ökologischen Fußabdruck ihrer Produkte zu verringern, und wichtige Ergebnisse erzielt.
Mehr als zwanzig Prozent beträgt der Anteil der Umweltinvestitionen der Unternehmen der Branche an den gesamten Bruttoinvestitionen in Sachanlagen: ein wirklich bedeutendes Datum, insbesondere im Vergleich zu den ISTAT-Daten, die sich auf beide Branchen als Ganzes beziehen (ca 1,5 %) und auf die Metallurgie im weitesten Sinne, d.h. bezogen auf den Ateco-Code 24, der in einem Bereich zwischen 3,5 und 4 % liegt.
Zahlen dieser Größenordnung zeigen deutlich, wie den Unternehmen der Branche inzwischen klar ist, dass Maßnahmen zur Verringerung der Umweltauswirkungen, die Gießereitätigkeiten mit sich bringen können, heute über die bloße Einhaltung der Umweltgesetzgebung hinaus entscheidend sind, um dies gewährleisten zu können wichtiger Wettbewerbsvorteil.
Die wachsende Sensibilität der Zivilgesellschaft und der öffentlichen Verwaltungen gegenüber diesen Themen und der Dekarbonisierung führt tatsächlich zur Entwicklung von Systemen zur Bewertung und Zertifizierung der ökologischen Nachhaltigkeit, die zunehmend nicht nur die Hersteller von Waren oder Dienstleistungen für den Verbraucher, sondern auch produzierende Unternehmen einbeziehen Zwischenkomponenten innerhalb von Zulieferketten, wie dies bei Gießereien der Fall ist.
Kreislaufwirtschaft: Der Einsatz von Recyclingmaterialien als Sekundärrohstoff nimmt zu
Die Gießerei ist ein zentrales Element des „Kreislauf“-Wirtschaftsmodells: Tatsächlich stellt die Schmelztätigkeit seit jeher die Technik dar, durch die es möglich ist, Schrott zu verwenden, um neue Produkte herzustellen. Als solches repräsentiert das Gießereiunternehmen die Essenz des Konzepts der Kreislaufwirtschaft, das den Abfall in den Mittelpunkt der Aktivitäten stellt, die auf seine wirtschaftliche Verwertung abzielen.
Nach den gesammelten Daten einer Stichprobe von Unternehmen, die 37 % der gesamten Produktion von Gussteilen in Italien ausmachen, ist in den letzten Jahren eine weitere leichte Zunahme der Verwendung von recycelten Rohstoffen zu verzeichnen.
NE-Metallgießereien verwenden zur Beschickung der Öfen ausschließlich Barren aus Aluminium oder anderen Leichtmetalllegierungen. Dies bedeutet jedoch nicht, dass der verwendete Rohstoff nicht aus dem Recycling stammt: Ein Großteil der von italienischen NE-Gießereien verwendeten Barren stammt tatsächlich aus dem Umschmelzen von NE-Schrotten aus dem Recycling durch Raffinerien. Darüber hinaus haben Gießereiprodukte, egal ob aus Eisen- oder Nichteisenmetallen, sehr lange Lebenszyklen und können am Ende ihrer Nutzung wiederum in einem ewigen, unerschöpflichen Kreislauf zu neuen Produkten recycelt werden.
Produktionsabfälle: Weniger Volumen und mehr Wiederverwendung für die Dekarbonisierung von Gießereien
Der Gießereisektor, insbesondere der mit Sandformanlagen, ist durch ein hohes Abfall/Nettoprodukt-Verhältnis gekennzeichnet. Die Aufmerksamkeit der Unternehmen der Branche hat sich in den letzten Jahren stark auf die Methoden zur Verwaltung der Rückstände der verschiedenen Arbeitsprozesse konzentriert, sowohl um ihre Mengen zu reduzieren, die Wiederverwendung innerhalb der Gießereiprozesse selbst zu fördern als auch um mögliche Alternativen zu erforschen externe Wiederverwendung zur traditionellen Entsorgungstätigkeit.
Sinnbildlich für den Trend zur Kreislaufwirtschaft in der Abfallwirtschaft ist der Fall der erschöpften Erde. Neben dem absoluten Rückgang der produzierten Mengen, die von rund 575 Kilogramm pro produzierter Tonne im Jahr 2000 auf 324 Kilogramm im Jahr 2019 (bei einer Reduzierung von mehr als 43 %) gingen, ist es interessant zu beobachten, wie derzeit mehr als 95 % der erschöpften Erde wird durch externe Wiederverwendungen in Verwendung als Rohstoffe als Ersatz für Sande und Erden aus der Gewinnung zurückgewonnen, wodurch die Notwendigkeit einer Deponierung praktisch entfällt.
Dieser Trend steht einmal mehr in voller Übereinstimmung mit den Prinzipien der Kreislaufwirtschaft, die darauf abzielt, Produktionsrückstände (Abfälle oder Nebenprodukte) als "Sekundärrohstoffe" aufzuwerten, die in industriellen Prozessen wie Zementfabriken und Hochöfen verwendet werden können , oder noch für die Herstellung von Bau- und Tiefbauprodukten.
Um diesen Trend weiter zu fördern, wurde von der Region Lombardei der Technische Tisch „Hüttenschlacke“ aufgestellt. Das Ziel dieser Initiative besteht darin, allen Beteiligten einen klaren und gemeinsamen technisch-regulatorischen Referenzrahmen für die Kreislaufwirtschaft einiger der wichtigsten Rückstände aus Eisen und Stahl und metallurgischen Aktivitäten in der Region bereitzustellen.
Klimaschädliche Emissionen: Auf dem Weg zur CO2-Neutralität
Laut der von Interconnector Energy Italia und den Confindustria-Verbänden in Zusammenarbeit mit der Boston Consulting Group erstellten Studie „Strategy for the decarbonisation of Hard to Abate sector“ sind die sieben energieintensivsten Industriesektoren (Stahl, Zement, Papier, Keramik, Chemikalien, Glas und Gießereien) verursachen insgesamt etwa 20 % der direkten Treibhausgasemissionen in Italien.
Auch wenn nur ein kleiner Teil dieser Emissionen auf Gießereien entfällt, haben sich die Unternehmen der Branche schon lange verpflichtet, ihre Emissionen klimaschädlicher Gase zu reduzieren, und werden in den kommenden Jahren einen weiteren und anspruchsvollen Weg gehen müssen , in technischen und wirtschaftlichen Verpflichtungen, im Hinblick auf die von Europa gesetzten Dekarbonisierungsziele, um genau einen Fahrplan der Maßnahmen zu skizzieren, die erforderlich sind, um bis 2050 CO2-Neutralität zu erreichen.
Tatsächlich wurde der Industrial DecarbonizationPact unterzeichnet, ein Bündnis für die Dekarbonisierung der Industrie, das darauf abzielt, einen schnellen und integrativen ökologischen Übergang zu gewährleisten, der nicht nur in der Lage ist, die von Brüssel angegebenen Ziele zu erreichen, sondern auch die Wettbewerbsfähigkeit der internationalen Märkte der vertretenen Sektoren zu erhalten das Rückgrat der italienischen Wirtschaft.
Aus technischer Sicht ist innerhalb der Gießereibranche das wichtigste Instrument, auf das man sich berufen kann, um die geforderten Dekarbonisierungsziele zu erreichen, die Elektrifizierung von Unternehmen. Der zweite Hebel in der Reihenfolge der potenziellen Auswirkungen betrifft die Verwendung von Biokraftstoffen in Gasöfen.
Nach Schätzungen der Studie der Boston Consulting Group wäre bis 2030 die vollständige Elektrifizierung von Kupolöfen, die Teilelektrifizierung (ca. 20 %) von Gasöfen und der Einsatz von Biobrennstoffen bei den restlichen 80 % der Gasöfen möglich eine Reduzierung der direkten CO2-Emissionen um ca. 50 %. Die vollständige Elektrifizierung der verbleibenden gasbefeuerten Öfen bis 2050 würde zu einer 90-prozentigen Reduzierung der bisher von den Unternehmen der Branche verursachten direkten Emissionen führen.
Der Ersatz des derzeitigen Ofenparks, der mit Energieträgern wie Koks und Methan betrieben wird, durch Elektroöfen erfordert nicht nur große wirtschaftliche Anstrengungen, die zwangsläufig durch spezifische finanzielle und/oder steuerliche Instrumente unterstützt werden müssen, sondern erfordert auch Interventionen um die benötigte Menge an Strom zu erzeugen; die studie schätzt in diesem zusammenhang, dass der strombedarf der schwierigen sektoren im jahr 2030 bei 64 tWh liegen wird, wovon etwa 40 % „grün“ sind.
Darüber hinaus sind für einen nachhaltigen Elektrifizierungsprozess wichtige regulatorische Eingriffe erforderlich, um den Strompreis wettbewerbsfähig zu machen, der derzeit in unserem Land einen erheblichen Preisabstand zu seinen europäischen Partnern aufweist, auch aufgrund unterschiedlicher Gebührenverwaltungssysteme beispielsweise an indirekte Energiekosten gekoppelt.
Staubemissionen: Drastisch reduziert dank neuer Technologien
Ein weiterer Aspekt, an dem die Unternehmen der Branche in den letzten Jahren kontinuierlich gearbeitet haben, sind die Staubemissionen: Gießereien, insbesondere solche, die „Einweg“-Sandumformverfahren einsetzen, erzeugen diese in allen Phasen des Produktionsprozesses, vom Guss bis zur Gussfertigbearbeitung . Auch bei der Dauerproduktion von NE-Metall-Gussteilen entstehen Partikelemissionen, beziffert als „Ölnebel“.
Durch den Einsatz von BVT-Techniken (Best Available Techniques) und die Entwicklung von End-of-Pipe-Technologien konnten wichtige Ziele zur Reduzierung von Restemissionen erreicht werden. Dieser Trend wurde auch im Zeitraum 2017-2019 mit durchschnittlich -12,5 % im Vergleich zu 2015 verzeichnet. Die Zahl ist noch signifikanter, wenn man bedenkt, dass das Emissionsniveau im Jahr 2015 wiederum um -65 % niedriger war als im Jahr 2015 2003.
Energie: Immer mehr Effizienzeingriffe
Die Frage des Energieverbrauchs für einen „energieintensiven“ Sektor ist nicht nur ein bedeutender Umweltaspekt, insbesondere in Bezug auf die Frage der Dekarbonisierung von Gießereien, sondern auch einer der Hauptkostenfaktoren für das Gießen.
Bei allen Arten von Gießereien nehmen die Schmelzaktivitäten den überwiegenden Anteil an Energie auf: Diese machen bei Gusseisengießereien 63 %, bei Stahlgießereien 54 % und bei Aluminiumgießereien 35 % aus. In dieser Phase des Prozesses können daher die bedeutendsten Effizienzmaßnahmen angesetzt werden, wie die Analyse der Daten des „Leitfadens zur Erstellung von Energiediagnosen im Gießereibereich“ zeigt, den Enea gemeinsam erstellt hat mit Assofond.
Der Leitfaden trägt dazu bei, das Bewusstsein für die Bedeutung von Energieeffizienz in der Branche zu schärfen, liefert Unternehmen einen konkreten Beitrag und ist Teil der Reihe „Energie-Effizienz-Notizbücher“. Es ist ein operativer Leitfaden sowohl für Unternehmen, die im Gießereisektor tätig sind, als auch für Fachleute, die an der Erstellung einer „Qualitäts“-Energiediagnose beteiligt sind und mit Anhang II des Gesetzesdekrets übereinstimmen 102/2014.
Die Veröffentlichung enthält die wesentlichen Energieverbrauchspositionen der Produktionsstandorte, die Hinweise zur Implementierung eines branchengerechten Überwachungssystems, die Energieleistungsindizes, die sich sowohl auf die gesamte Anlage als auch auf einige Prozesse beziehen, und schließlich eine breite Übersicht über die mögliche Energieeffizienz-Interventionen, die in der wissenschaftlichen und technischen Literatur enthalten sind, zusammen mit einer wirtschaftlichen und energetischen Bewertung der durchgeführten und vorgeschlagenen Interventionen, die in den letzten Jahren in den von Enea erhaltenen Energiediagnosen berichtet wurden.
Gerade die zu den Diagnosen durchgeführten Analysen ermöglichten es, die Energieeinsparungen zu quantifizieren, die von den Unternehmen der Branche im Anschluss an die durchgeführten Energiediagnosen identifiziert und erzielt wurden. Dies sind wichtige Einsparungen, die sich bezogen auf den einzusparenden Stromverbrauch auf insgesamt 86.800 MWh belaufen, was dem Jahresverbrauch von 32.134 typischen Familien entspricht. Die 370 tatsächlich durchgeführten Eingriffe hingegen haben es den Unternehmen der Branche ermöglicht, insgesamt rund 2.800 TOE (Tons of Oil Equivalent) pro Jahr einzusparen.
Quelle: In Fonderia – ll magazine dell’industria fusoria italiana